氢气有望在未来成为我国重要的能源之一,使用范围较广。
储氢技术作为氢气从生产到利用过程中的桥梁,是指将氢气以稳定形式的能量储存起来,以方便使用的技术。
不同的储氢技术对氢气的运输方式和使用成本都有重要影响,下面我们将不同的储氢技术进行介绍。
首先我们将主要的储氢方式分为物理储氢技术、化学储氢技术和其他储氢技术。
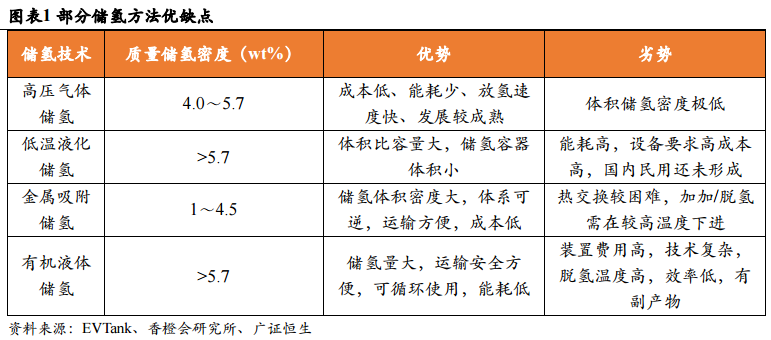
物理储氢技术:目前高压气态储氢应用最广泛
物理储氢技术是指单纯的通过改变储氢条件提高氢气密度,或通过物理吸附作用将氢气储存在金属合金等储氢材料中的技术。
其中,高压气态储氢是目前发展最成熟、应用最广泛的物理储氢技术。
高压气态储氢:技术最成熟、使用最广泛
高压气态储氢技术是指在高压条件下,将氢气压缩并注入储氢瓶中,让氢气以高密度气态形式储存的一种技术。
国外研究表明,氢气质量密度随压力增加而增加,在30~40MPa时,氢气质量密度增加较快,而压力70MPa以上时,氢气质量密度变化很小。
因此大多储氢瓶的工作压力在35~70MPa范围内。
目前,高压气态储氢瓶根据其材料不同主要分为四种类型:纯钢制金属瓶(I型)、钢制内胆纤维缠绕瓶(II型)、铝内胆纤维缠绕瓶(III型)和塑料内胆纤维缠绕瓶(IV型)。
由于前两种储氢瓶的质量储氢密度较低,且氢脆问题严重(氢脆是溶于钢中的氢,聚合为氢分子,造成应力集中,超过钢的强度极限,在钢内部形成细小裂纹的现象),难以满足车载储氢系统的要求。
因此车载储氢瓶主要是用后两种类型的储氢瓶。III型、IV型瓶由内胆、碳纤维强化树脂层及玻璃纤维强化树脂层组成,气瓶质量较轻,单位质量储氢密度有所提高。
目前国外已经实现IV型储氢瓶在车用领域70MPa的应用,但国内IV型储氢瓶使用受到限制。
国内目前主要以35MPaIII型瓶为主,但70MPaIII型瓶的使用标准已经在2017年发布的GBT35544—2017《车用压缩氢气铝内胆碳纤维全缠绕气瓶》中有所规定,并开始在轿车中小范围的使用。
固定式高压气态储氢主要应用在固定场所,如制氢厂、加氢站以及其他需要储存高压氢气的地方。目前主要使用大直径储氢长管和钢带错绕式储氢罐来储氢。
大直径储氢长管方面,石家庄安瑞科气体机械有限公司2002年在国内率先研制成功20/25MPa大容积储氢长管,并应用于大规模氢气运输。
继而开发的45MPa储氢瓶组,已成功用于国内众多加氢站。长管气瓶材料为铬钼钢4130X,强度高,具有良好的抗氢脆能力。
钢带错绕式储氢罐目前有45Mpa和98Mpa两种型号,如浙大与巨化集团制造生产的两台国内最高压力等级98MPa立式高压储罐,安装在江苏常熟的丰田加氢站中。
尽管高压气态储氢是目前使用最广泛且技术最成熟的技术,但其缺点在于储氢量太少,体积比容积低。
即使是太空用的钛瓶,其储氢重量也仅为瓶重量的5%。并且高压气态储氢受压力和储氢瓶材料影响较大,且安全性能相对较差,有泄漏、爆炸等安全隐患。
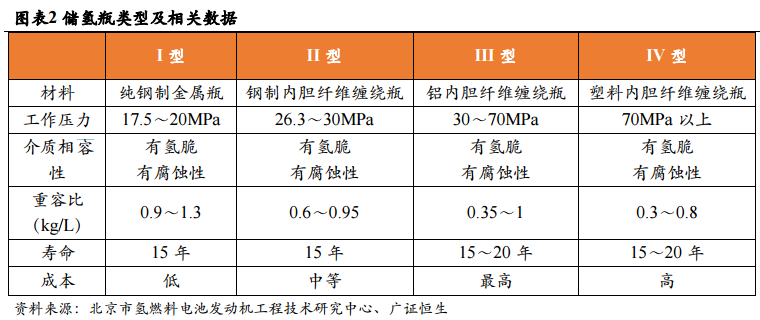
低温液态储氢:未来重要发展方向
低温液态储氢是将氢气压缩后冷却到-253摄氏度以下,使之液化并存放在绝热真空储存容器中的一种储氢技术。
由于液态氢具有很高的密度,在常温、常压下液氢的密度是气态氢的800倍以上,因此将氢气液化后能够使得储运简单,且体积比容积大。
但其缺点在于,将气态的氢气转化成液态的氢气较困难,根据一览众咨询的调研,要液化1kg的氢气需要消耗4-10千瓦时的电量,并且为了储存液态氢气,需要能够耐受和保持超低温的特殊容器,因此成本高昂。
目前,国外有70%左右的氢气通过液态形式运输,日本、美国、德国等国家已经将液氢的运输成本降低到高压氢气的八分之一左右。
然而目前国内技术还未成熟、设备成本高且暂时缺乏液氢相关的技术标准和政策规范,因此国内布局液氢的企业较少,应用还仅限于航天行业,在民用方面还未实现使用。
但根据国外已有经验,低温液态储氢将是未来重要的发展方向,且发展空间大。
为了避免或减少氢气的蒸发损失,低温液态储氢技术不仅对液态储氢罐的材质有要求,还需要配套的严格的绝热方案和冷却设备,因此低温液态储氢罐容积一般较小,氢气质量密度为10%左右。
液态储氢罐一般分为内外两层,内胆承装低温的液氢通过支撑物放置在外壳中心,支撑物可由玻璃纤维带支撑,具有良好的绝热性能。
夹层中间填充多层镀铝涤纶薄膜,以减少热辐射,在薄膜之间可以放绝热纸来增加热阻同时吸附低温下的残余气体。之后用真空泵抽取夹层内的空气制造高真空状态来避免气体对流漏热。
一般情况下,储氢罐内胆使用铝合金、不锈钢等材料制成,外壳使用低碳钢、不锈钢等材料,也可以使用铝合金材料来减轻容器重量。
目前,世界上最大的低温液态储氢罐位于美国的肯尼迪航天中心,其容积高达1120000L。
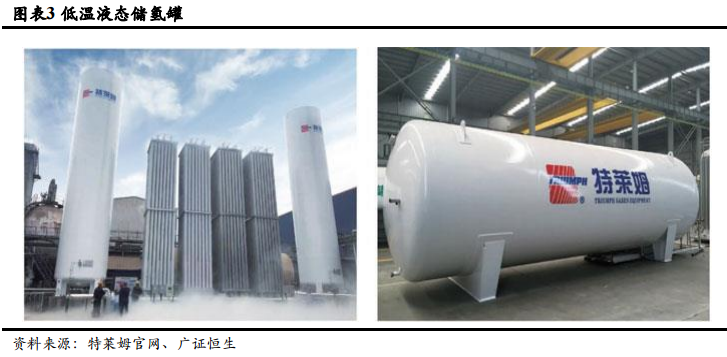
化学储氢技术:处于技术攻克阶段
化学储氢技术是利用储氢介质在一定条件下能与氢气反应生成稳定化合物,再通过改变条件实现放氢的技术,主要包括有机液体储氢、液氨储氢、配位氢化物储氢、无机物储氢与甲醇储氢。
有机液态储氢:优点明显但技术难度高
有机液态储氢技术基于不饱和液体有机物在催化剂作用下进行加氢反应,生成稳定化合物,当需要氢气时再进行脱氢反应。
常用的不饱和液体有机物及其性能如下。
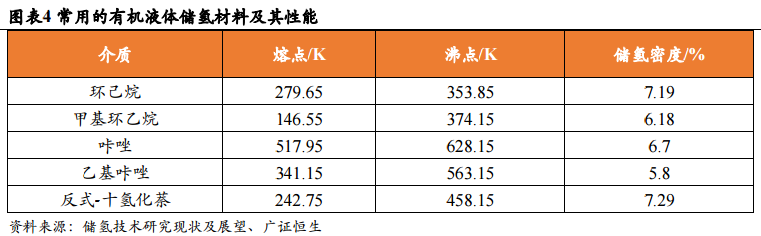
有机液体储氢技术具有较高储氢密度,通过加氢、脱氢过程可实现有机液体的循环利用,成本相对较低。
同时,常用材料(如环己烷和甲基环己烷等)在常温常压下,即可实现储氢,安全性较高;催化加氢和脱氢反应可逆,储氢介质可循环使用。
该方法便与大量的储存和运输,安全性能好。
然而有机液体储氢也存在很多缺点,例如,必须配备的加氢、脱氢装置成本较高;脱氢反应效率较低且易发生副反应使氢气纯度不高;脱氢反应常在高温下进行,催化剂易结焦失活等问题。
并且由于冷启动和补充脱氢反应能量需要燃烧少量有机化合物,因此该技术很难实现“零排放”目标。
有机液体储氢技术在中国已有所成就,2017年,中国扬子江汽车与氢阳能源联合开发了一款城市客车,利用有机液体储氢技术,加注30L的氢油燃料,可行驶200km。
并且有机液体储氢技术的理论质量储氢密度最接近DOE的目标要求,提高低温下有机液体储氢介质的脱氢速率与效率、催化剂反应性能、改善反应条件、降低脱氢成本是进一步发展该技术的关键。
其他化学储氢技术:研发难度大但极具前景
液氨储氢技术是将氢气与氮气反应生产液氨,将液氨作为氢能的载体进行利用。液氨在常压、400℃条件下即可得到氢气,常用的催化剂包括钌系、铁系、钴系与镍系,其中钌系的活性最高。
2015年,液氨首次作为直接染料用于燃料电池中,其燃烧发电效率为69%,与液氢系统效率70%相近。
液氨储氢技术优点在于,液氨燃烧产物为氮气和水,对环境无害且液氨的储存条件较为温和;其缺点在于,有报告称,体积分数仅为1×10-6的未分解液氨混入氢其中,就会造成染料电池的严重恶化。
配位氢化物储氢是利用碱金属与氢气反应生成离子型氢化物,之后在一定条件下分解出氢气的技术。
最初的配位氢化物是由日本研发的氢化硼钠和氢化硼钾,但这两种氢化物存在脱氢过程中温度较高等问题,因此进一步研发了以氢化铝络合物为代表的新一代配合物储氢材料。
目前主要的研发方向是改善配位氢化物低温放氢性能和对材料进行回收再利用。
甲醇储氢技术是指将一氧化碳与氢气在一定条件下反应生成液体甲醇,将其作为氢能的载体进行利用。
在一定条件下,甲醇可分解得到氢气用于燃料电池,同时,甲醇还可直接用作燃料。
2017年,北京大学的科研团队研发出一种铂-碳化钼双功能催化剂,可以使甲醇与水反应,释放出甲醇中的氢并活化水中的氢,从而得到更多的氢气。
此外,甲醇的储存条件为常温常压,方便运输。
其他储氢技术
除了常见的物理储氢技术和化学储氢技术外,还有一些其他类型的储氢技术,在这部分主要介绍吸附储氢和水合储氢两种储氢技术。
前者是利用吸附剂与氢气作用,实现高密度储氢;后者是利用氢气生成固体水合物,提高单位体积氢气密度。
吸附储氢技术:技术待提高,发展前景好
吸附储氢所利用的吸附材料主要包括金属合金、碳质材料和金属框架物等。
金属合金储氢是利用吸氢金属A和对氢不吸附或吸附量较小的金属B制成合金晶体,在一定条件下,金属A作用强,氢分子被吸附进入晶体,形成金属氢化物。
之后通过改变条件,减弱金属A的作用,实现氢分子的释放。
其中A金属多为镁、钛或稀土元素,B金属多为铁、钴、镍和铜铝等。金属合金储氢的特点是氢以原子状态储存于合金中,安全性较高。
但这类材料的氢化物过于稳定,热交换比较困难,加氢和脱氢过程只能在较高温度下进行。
相同体积下,固态低压合金储氢装置,压力降低为高压气瓶的1/7,有效储存的氢气质量为高压气瓶的3倍。常用的金属合金类型及其代表物如下。
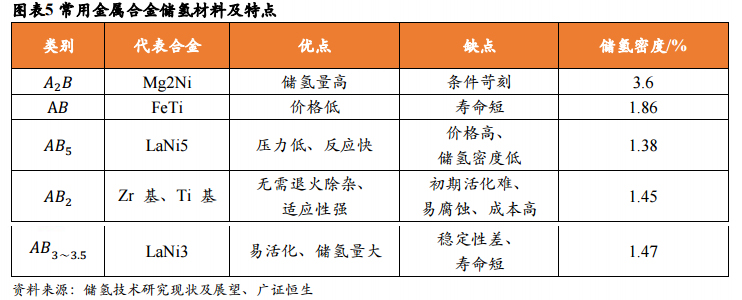
除此之外,碳质材料也可以作为氢气的吸附材料。一些碳质材料,如表面活性炭、石墨纳米纤维、碳纳米管等,在一定条件下对氢的吸附能力较强,因此可以用于吸附储氢。
碳质材料由于具有较大的比表面积以及强吸附能力,氢气质量密度普遍较高。
同时,碳质材料还具有质量轻、易脱氢、抗毒性强、安全性高等特点。但目前碳质材料吸附还存在缺点,例如机理认识不完全、制备过程较复杂、成本较高等。
预计未来的研究方向主要集中在相关机理的研究;制备、检测工艺的优化;高储量、低成本碳材料的探索以及生产过程的大规模工业化等方面。常用的碳质材料及其储氢特点如下。
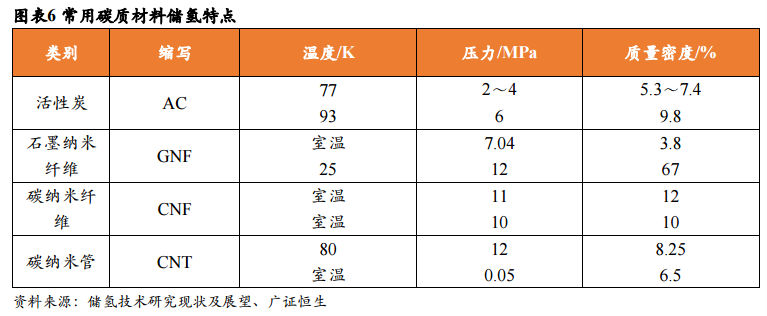
水合物法储氢技术
水合物法储氢技术是指将氢气在低温、高压的条件下,生成固体水合物进行出巡。由于水合物在常温、常压下即可分解,因为,该方法的脱氢速度快且能耗低。
同时,水作为其储存介质,具有成本低、安全性高等特点。不同类型水合物储氢所要求的压力和温度都不相同,具体实践时需要区分操作。
然而水合物法储氢技术虽然在理论上可行,但实验结果表示其储氢密度未达到预期。
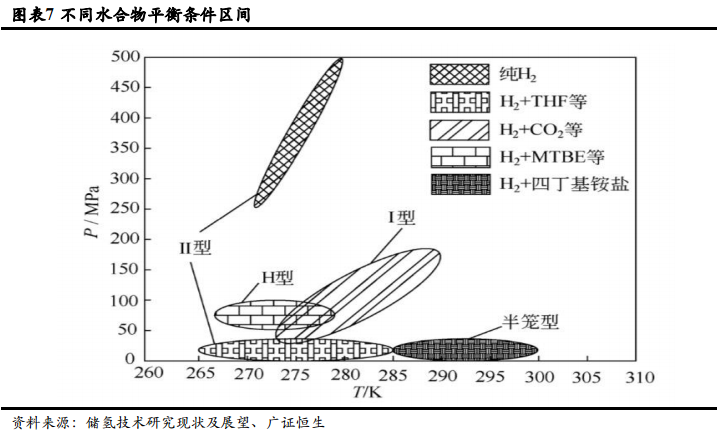
根据上述对于物理、化学和其他储氢方法的讨论,从整体发展情况来看,我们认为目前国内的储氢技术发展相对落后,高压气态储氢技术落后较大,储氢量低得多。
具体表现在,国外已经将70MPa的储氢罐已应用到燃料电池汽车上,而国内的储氢罐关键材料仍依赖进口。
低温液氢技术、吸附储氢技术与国外先进水平存在较大差距,产业化相距甚远。
从技术成熟方面来看,高压气态储氢最成熟、成本最低,是现阶段主要应用的储氢技术,在基本能与传统加油方式相媲美,但对于更高的车载储氢要求如储氢量、安全性等,高压气态储氢技术难以满足需求。
从质量储氢密度上看,有机液体储氢质量储氢技术密度相对较高,但目前存在成本高等问题。
从成本方面来看,金属氢化物储氢及有机液体储氢成本均较高,还处于攻克研发阶段,不适合目前小批量的应用。
预计未来化学方法储氢是重要的发展方向,除此之外,复合储氢技术,如低温高压储氢技术和高压金属氢化物储氢罐,也逐渐被企业考虑和使用。
