自从氢能被总理在政府工作报告上提及后,氢燃料电池行业近来貌似如火如荼,但是膜电极作为燃料电池电堆最关键的一环,国内会存在哪些问题呢?与国际上的领先企业相比差距大吗?
以下是困扰中国膜电极发展的主要的几个问题。
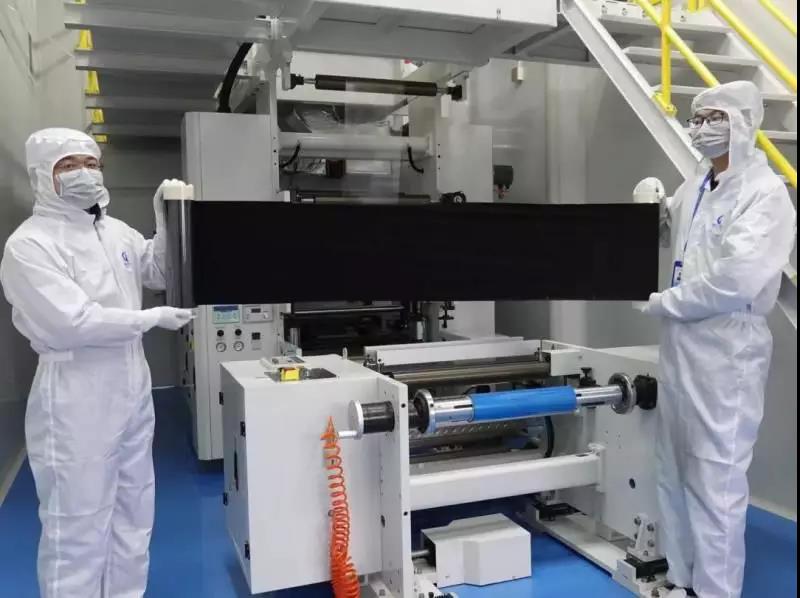
苏州擎动膜电极
一、关键材料问题
催化层
质子交换膜燃料电池中膜电极组件(MEA)是整个电池的核心,目前MEA中的催化层绝大部分采用铂(Pt)作催化剂,在EMA中铂催化剂大多为负载型催化剂,这些负载型超细铂催化剂具有金属颗粒小、分散度高、活性表面积大和表面能高的特点,因而具有独特的催化性能。
在燃料电池中铂作为催化活性中心,其含量直接影响电极的电催化性能和电池的性能及成本。铂是贵金属,资源有限,其成本不会随着规模的扩大而成本降低,甚至可能上升。
因此,需要从技术层面尽可能地降低Pt用量,同时保证膜电极寿命不受影响,这是一个难点。
能链采访了武汉理工氢电的总经理田明星,他介绍说目前很多研究机构都在研究无铂(Pt)技术,如武汉理工氢电的技术支撑方武汉理工大学也有许多教授在做非Pt催化剂研究。
武汉理工氢电认为,目前非Pt催化剂在车用方面,商业化的可行性比较低,但非Pt是未来理想的目标,但短期内在商业化产品上没有想象中那么快,所以短期内还是以低Pt作为技术路线。低铂和无铂催化剂是未来技术发展方向。
目前国内技术水平下催化层中的铂载量为0.5g-0.8g/kw,而国际领先的企业已经能够做到0.3g-0.5g/kw,美国能源局的目标是,到2020年铂用量降至每千瓦0.125g。
扩散层
在质子交换膜燃料电池中,气体扩散层主要作用是为参与反应的气体和生成的水提供传输通道、支撑催化剂。
作为膜电极关键组成材料之一,其国产化突破与量产,对中国燃料电池成本降低与推广应用具有重要价值。气体扩散层由基底层和微孔层组成,其中基底层材料大多是多孔炭纸或碳布,微孔层通常由导电炭黑和憎水剂构成。
目前全球碳纸/碳布生产厂家较少,供应商主要为日本东丽、德国西格里集团、日本JSR、加拿大Ballard、台湾碳能等。
其中,东丽占据较大的市场份额,我国对碳纸的研发主要集中于中南大学、武汉理工大学等高校。
中国大陆气体扩散层量产技术还是空白,主要原因是气体扩散层的石墨化工序需要2000°C以上的高温,但高温炉技术尚未掌握。
质子交换膜
质子交换膜的性能直接影响燃料电池的稳定性和耐久性。
质子交换膜的主要作用有两个:一方面为电解质提供氢离子通道,一方面作为隔膜隔离两极反应气体。此外,质子交换膜还需要对催化剂层起到支撑作用。
质子交换膜类型主要包括全氟磺酸质子交换膜、非全氟化质子交换膜、无氟化质子交换膜、复合膜以及高温膜。目前,最广泛应用的质子交换膜为戈尔的select膜。
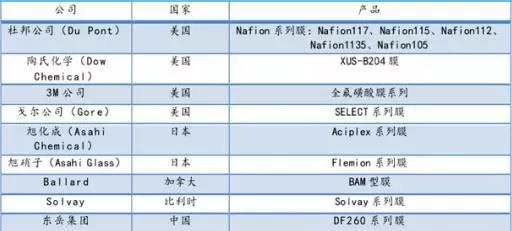
国内外主要质子交换膜生产厂家及产品( 来源:国家统计局等公开来源)
国内新源动力和东方电气近来推出的燃料电池电堆都采用了国外戈尔公司的GORE-SELECT®质子交换膜。(戈尔是全球领先的质子交换膜燃料电池技术供应商。GORE-SELECT®质子交换膜成为满足汽车严苛应用的标准,这款质子交换膜早已应用于其他的商业燃料电池汽车,如丰田的MIRAI和本田的CLARITY FUEL CELL。)
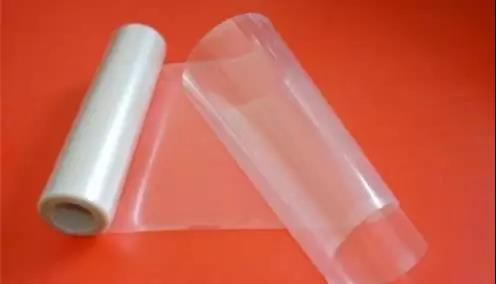
东岳集团全氟磺酸质子交换膜示意图
目前国内能够批量化供应质子交换膜的企业只有山东东岳,其他企业多数都在研发或者小批量试产阶段。
二、制备技术问题
膜电极技术目前经历了几代革新,大体上可以分为热压法、CCM法和有序化膜电极三种类型。
第一代的膜电极制备工艺主要采用热压法,具体是将催化剂浆料涂覆在气体扩散层上,构成阳极和阴极催化层,再将其和质子交换膜通过热压结合在一起,形成的这种膜电极称之为“GDE”结构膜电极。
采用热压法优点:膜电极的通气性能良好,制备过程中质子交换膜不易变形。
采用热压法缺点:催化剂涂覆在气体扩散层上,易通过孔隙嵌入到气体扩散层内部,造成催化剂的利用率下降,并且热压粘合后的催化剂层和质子交换膜之间粘力较差,导致膜电极总体性能不高。
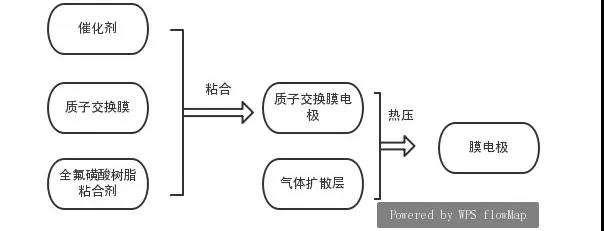
第二代的膜电极制备技术是催化剂直接涂膜技术(见上图),具体是将催化层直接涂覆在质子交换膜的两侧,再通过热压的方式将其和气体扩散层结合在一起形成“CCM”结构膜电极。
该技术提高了催化剂的利用率,并且由于使用质子交换膜的核心材料作为粘结剂,使催化层和质子交换膜之间的阻力降低,提高了氢离子在催化剂层的扩散和运动,从而提高性能,是目前的主流应用技术。
但是第二代膜电极制取方法还存在着反应过程中催化层结构不稳定,Pt颗粒易脱落的问题,影响着膜电极的使用寿命。
针对该现象,各大研究机构结合高分子材料技术及纳米材料技术,向催化层的有序化方向发展,制成的有序化膜电极具有优良的多相传质通道,大幅度降低了膜电极中催化剂Pt的载量,并提升了膜电极的性能和使用寿命。
膜电极结构的有序化使得电子、质子气体传质高效畅通,对于提高发电性能和降低PGM的载量提供了新的解决方案,有序化膜电极是下一代膜电极制备技术的主攻方向。
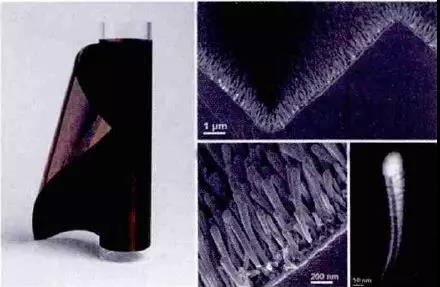
3M公司有序化膜电极及NSTF催化剂层形貌
目前国内企业采用的主要是CCM生产工艺,与国外相比,国外膜电极制备技术已经开发多年,甚至3M公司已经开发出了可量产的有序化膜电极技术,国内膜电极制备技术目前还有很大的提升空间。
国际膜电极的主要制造商是GORE,庄信万丰,Ballard,Greenerity等。
国内膜电极供应商主要是武汉理工新能源,其产品主要供应美国PlugPower公司。大连新源动力的膜电极产品主要是为上汽的发动机配套。
现阶段来看,国产膜电极性能与国际水平接近,但专业特性上如铂载量等性能与国际水平还有一定差距。
三、成本问题
产业化问题——现在要做出膜电极的样品,对于很多国内企业l来说并不是一件非常难的事情,难的是怎么实现几十万、几百万件的批量生产,生产的一致性、生产工艺水平高低都是会影响产品性能和成本的。
为了实现核心技术的自主可控,自2015年以来,全国各地纷纷出台政策,鼓励企业发展燃料电池产业,在产业环境与政策利好双重支撑下,中国的燃料电池产业链上的企业从无到有,从下游向上游进发。
而在《中国制造2025》里面更是提出,到2030年,要实现燃料电池高品质关键材料、零部件国产化和批量供应,燃料电池膜电极成本≤50元/kW。
(来源:能链)